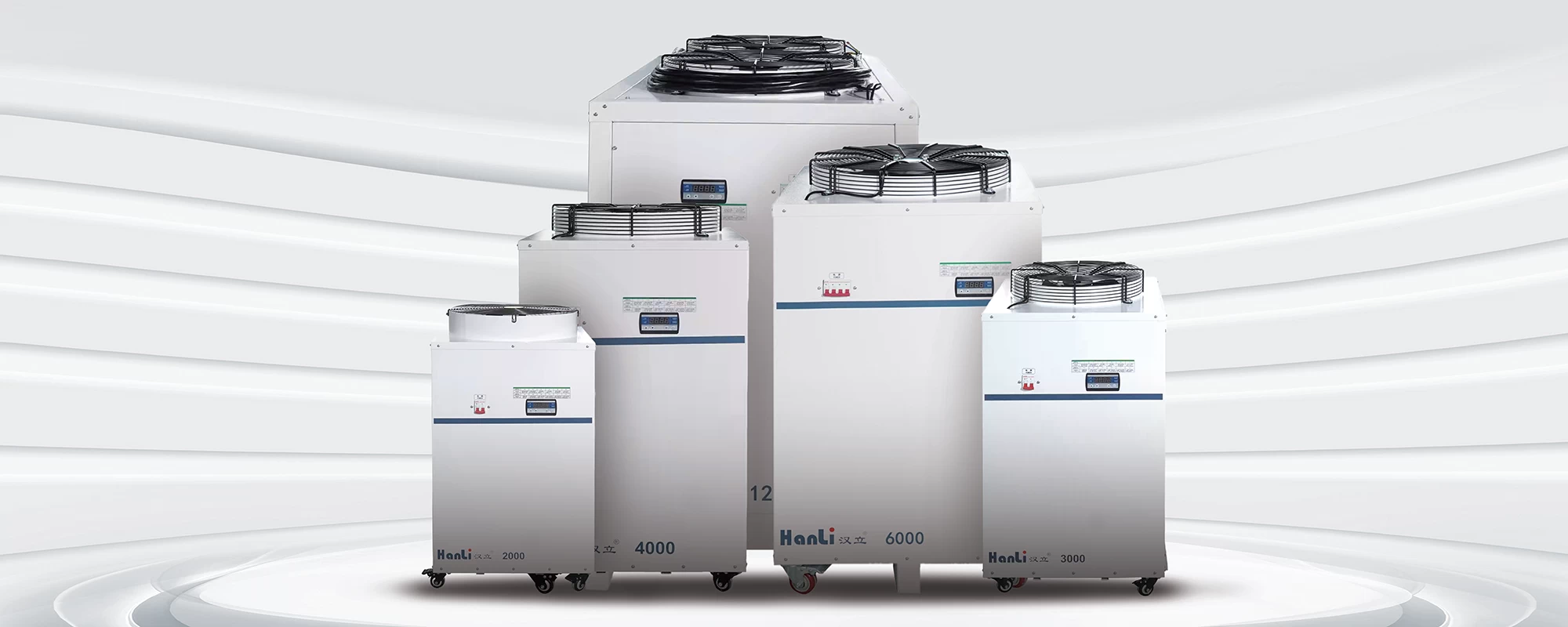
In fiber laser processing equipment, the laser is often referred to as the “heart,” so what could be considered the “blood vessels” of the equipment? If we classify the components by their functions, the answer would undoubtedly be the laser water chiller. The chiller not only cools the laser but is also crucial for cooling the cutting head. Today, let’s talk about the working principle, daily maintenance, and usage precautions of the laser water chiller, the “blood vessels” of fiber laser processing equipment.
1 Why do Laser Machines Need a Water Chiller?
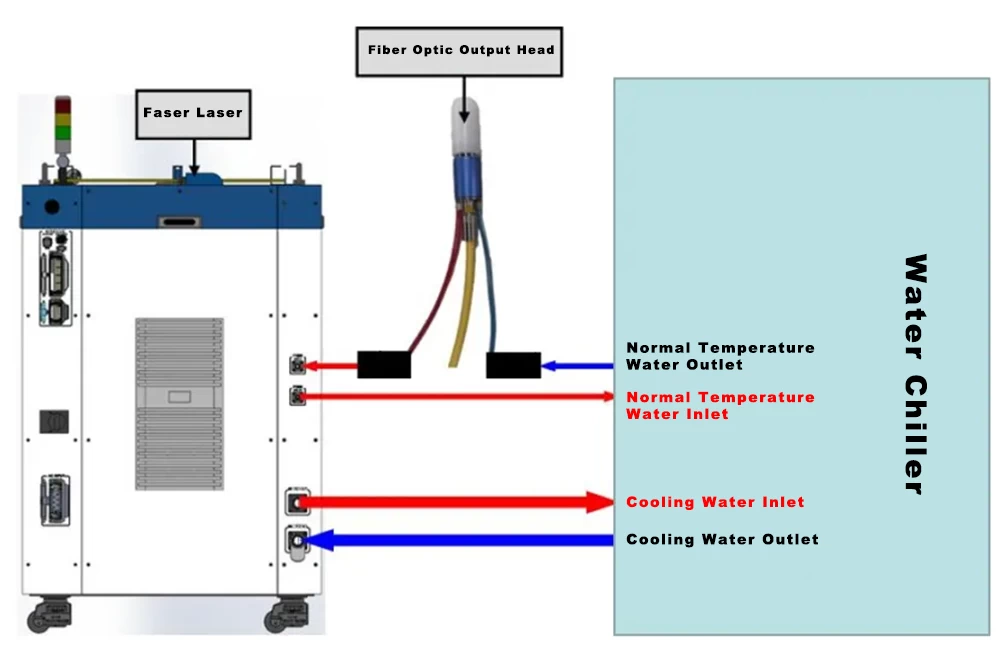
Schematic Diagram of the Laser Equipment Cooling System
The main working principle of a laser device is to convert electrical energy into light energy. Since this conversion is not 100% efficient, part of the electrical energy is transformed into heat. Additionally, the operation of the device and the friction of metals generate significant amounts of heat in the laser cutting head.
If this heat remains in the laser and cutting head, it can not only affect the processing results but, in severe cases, cause damage to internal components. As we all know, the laser and cutting head are costly, and the repair and replacement costs can be very high if damaged.
By using a water cooling system, the equipment’s loss rate can be effectively reduced, lowering maintenance costs.
2 How does the Laser Water Chiller Work?
A laser chiller, also known as a water cooler, is a device that provides constant temperature, flow, and pressure for cooling water. There are two main types: air-cooled and water-cooled chillers. In laser processing equipment, the water-cooled chiller is commonly used. A typical laser equipment chiller provides two stable-temperature cooling mediums: one to cool the laser and the other to cool the cutting head.
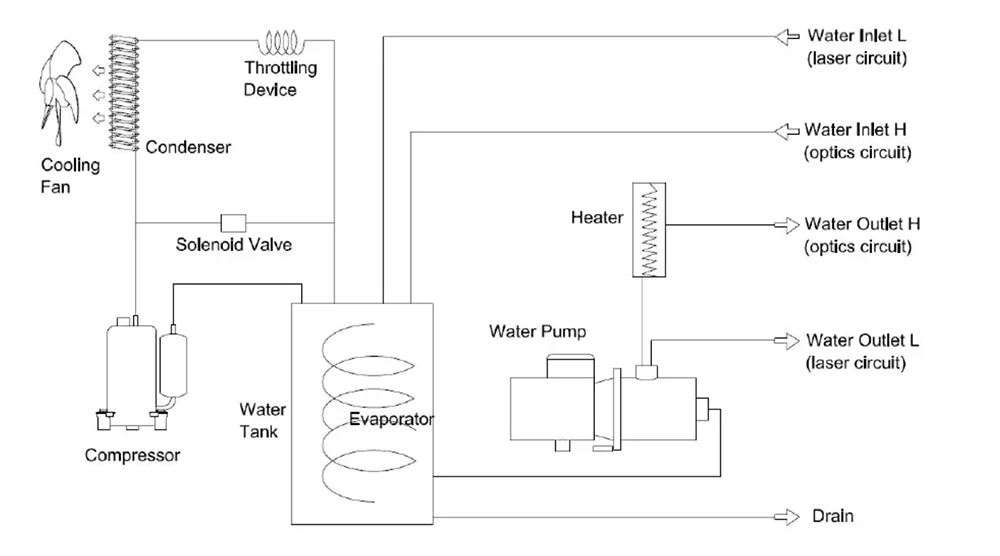
Principle Diagram of the Laser Water Chiller
The main working principle of a laser chiller is to convert electrical energy into mechanical energy. The built-in compressor compresses overheated steam into high-temperature, high-pressure gas, which is then sent into the condenser to be converted into high-pressure liquid. The liquid is then depressurized through a throttling device (such as an expansion valve or capillary tube), turning it into low-temperature, low-pressure subcooled liquid. This subcooled liquid enters the evaporator, absorbs heat, and vaporizes, becoming overheated steam again. It then returns to the compressor to start the next cycle, thereby achieving cooling.
3 Daily Maintenance of the Laser Water Chiller
3.1 Routine Checks
- Check the water level in the chiller tank weekly to ensure it meets the required level.
- Check the water quality of the chiller monthly (e.g., changes in color, smell, or presence of impurities).
3.2 Regular Cleaning and Replacement
The following cleaning and replacement intervals are recommended:
Filter cleaning cycle: Depending on water quality, check the laser’s water inlet and the chiller filter for blockage every week.
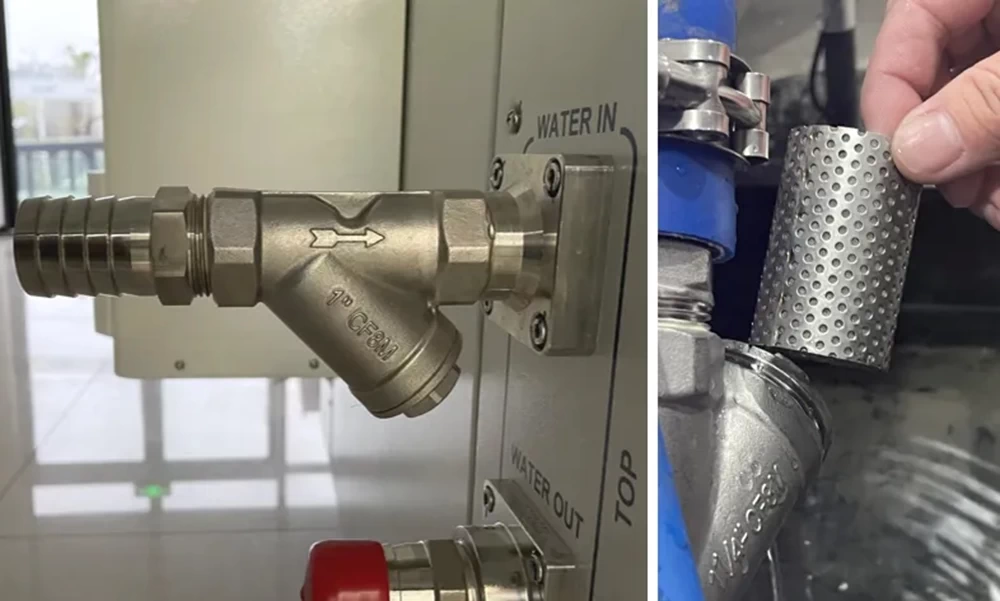
Laser Inlet Water Filter
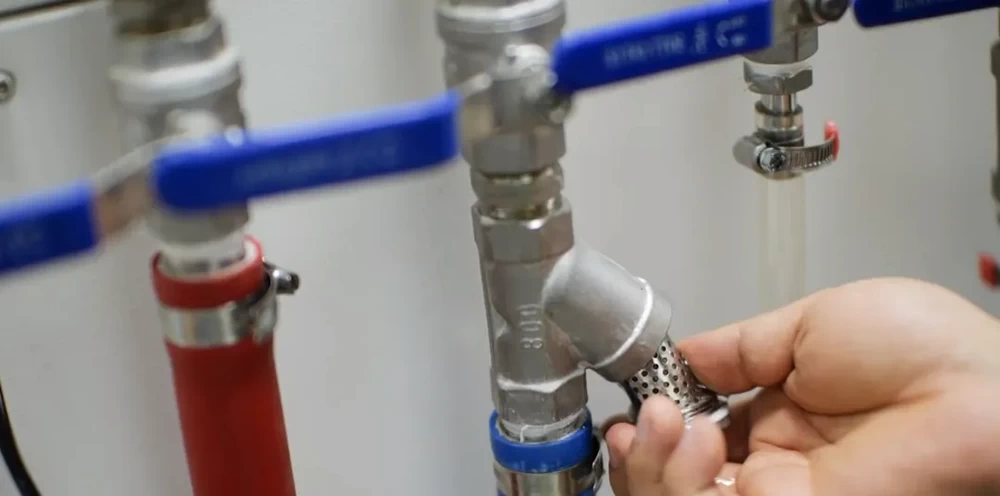
Remove the Chiller Filter
Dust Screen Cleaning Cycle: The dust screens on both sides of the chiller should be cleaned regularly. Use an air gun to blow away dust, and for oily dirt, use a mild detergent to clean. After cleaning, rinse and dry thoroughly.
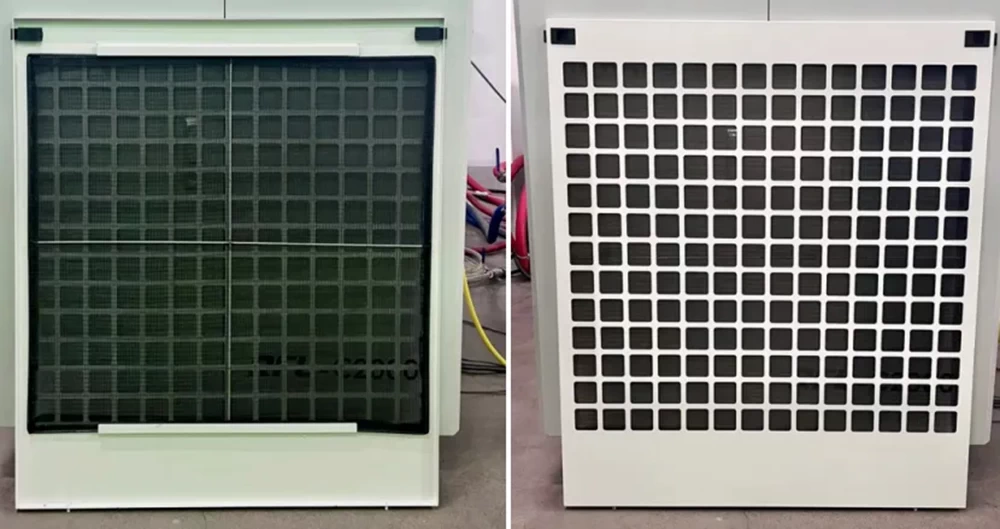
Dust Screen of the Laser Chiller
Filter Replacement Cycle: Check if the chiller filter is contaminated. Generally, filters should be replaced every six months.
Cooling Water Replacement Cycle: Replace the cooling water every three months at the latest, depending on water quality. Since the chiller’s tank is not sealed, prolonged exposure to dust can lead to water quality deterioration, resulting in undissolved substances adhering to the inner walls of the water path, obstructing water flow, and reducing cooling efficiency.
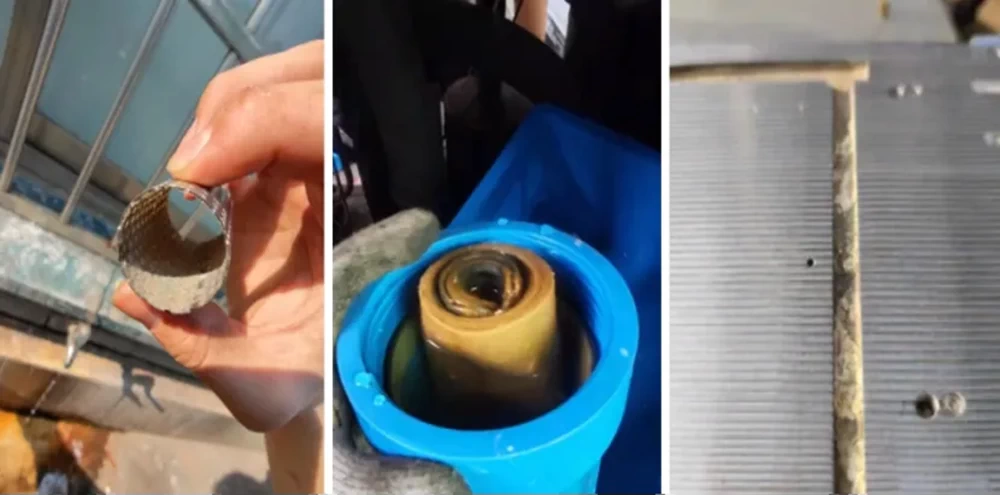
Polluted Filters, Filter Cartridges, and Laser Water Inlet
3.3 Steps for Replacing Cooling Water
- Disconnect the power supply to the equipment and chiller.
- Drain the water from both the chiller and the laser, and clean the water tank.
- Clean the filters, filter cartridges, and laser inlet filters.
- Fill the tank with distilled water until it reaches the standard liquid level.
- Start the chiller and check the water level, ensuring smooth water circulation.
Note:
- To prevent bacterial and algae growth, add 10% alcohol to the cooling water.
- It is recommended to use distilled or deionized water because these types of water are less likely to form scale during the heating cycle.
4 Special Maintenance Precautions for the Chiller
Low-temperature Environment Maintenance
When the environmental temperature drops to 0°C or lower, it is recommended to add antifreeze to the cooling water to lower the freezing point and prevent freezing. However, antifreeze should only be used for short periods, as long-term use can cause corrosion to the laser and cutting head’s optical components. After winter, the water lines should be cleaned with distilled or deionized water, and these types of water should be used as cooling fluids moving forward.
Precautions for Long Periods of Idle Time
If the equipment is not used for an extended period (e.g., during the Christmas holidays or before shipping), the cooling water in the chiller and laser should be drained, and compressed air should be used to blow out any residual moisture in the equipment to prevent freezing or leakage, avoiding potential equipment damage.

Draining the Cooling Water from the Chiller
Share The Post Now:
You Might Also Like
Yupec Laser is a leading provider of advanced fiber laser solutions in Europe, specializing in the sales, technical support, and service of Raycus fiber lasers.
With years of experience and a team of industry experts, we will be happy to help you with all your laser and laser application needs.
For more information about our products and services, please feel free to get in touch with us. We look forward to collaborating with you and driving innovation together.